Revolutionizing Affordable and Sustainable Housing Solutions
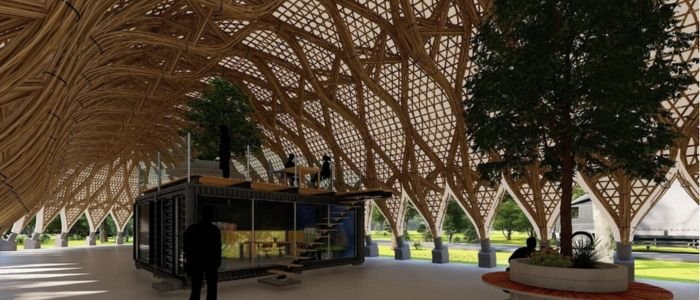
These homes offer speed, cost-efficiency, and eco-conscious benefits that are truly revolutionizing affordable and sustainable housing solutions. 3D-printed houses are no longer a distant vision; they are a tangible reality that offers innovative solutions to many of the housing sector’s challenges. This article will explore the benefits, real-world applications, and transformative impact of 3D-printed homes on affordable and sustainable living.
Understanding 3D-Printed Houses
3D-printed houses are structures built using additive manufacturing techniques, where layers of material are deposited to form walls and other components. This method contrasts sharply with traditional construction, where materials are assembled through manual labor and conventional machinery.
The primary materials used in 3D printing homes include concrete, clay, and specialized composites. These materials are extruded through a nozzle, layer by layer, to create the desired structure. The process is guided by digital blueprints, allowing for precision and customization in design.
Benefits of 3D-Printed Houses
As the demand for eco-conscious living grows, 3D-printed houses have become central to revolutionizing affordable and sustainable housing solutions. Their reduced material waste, lower labor costs, and energy-efficient designs offer a compelling alternative to traditional construction.
Cost Efficiency
One of the most significant advantages of 3D-printed houses is their affordability. Traditional construction involves costly materials, labor, and prolonged timelines. However, 3D printing minimizes these costs. Companies like Apis Cor have built homes for under $10,000, making homeownership accessible for more people.
Moreover, the reduction in labor needs and material waste drives these cost savings. With 3D printing, builders can optimize material use and reduce construction waste, which ultimately lowers the price of building a home.
One of the most compelling advantages of 3D-printed houses is their cost-effectiveness. Traditional construction methods involve significant labor costs, material wastage, and extended timelines. In contrast, 3D printing reduces labor requirements and material waste, leading to substantial cost savings. For instance, companies like Apis Cor have demonstrated the feasibility of constructing homes for under $10,000, making homeownership more accessible to a broader population.
Speed of Construction
3D printing dramatically shortens the building timeline. In some cases, construction can be completed within 24 to 48 hours. Traditional homes take months to build. For instance, Habitat for Humanity constructed a 1,200-square-foot home in just 28 hours using a 3D printer. This speed is especially beneficial in disaster relief situations or when affordable housing is urgently needed.
This rapid construction also contributes to less disruption in local communities, allowing people to move in quickly without long waiting periods.
The rapid construction capabilities of 3D printing are another significant benefit. While traditional homes can take several months to build, 3D-printed houses can be completed in a fraction of that time. For example, Habitat for Humanity constructed a 1,200-square-foot home in just 28 hours using a 3D printer, highlighting the potential for quick deployment in areas with urgent housing needs.
Design Flexibility
3D printing offers unmatched flexibility in design. Builders and architects can create complex, personalized structures without significant cost increases. This flexibility opens up new opportunities for creating homes that meet specific needs or unique aesthetics. The possibilities are nearly limitless when compared to the rigid constraints of traditional building materials.
3D printing offers unparalleled design flexibility. Architects and builders can create complex, custom designs that would be challenging or impossible with traditional methods. This capability allows for innovative architectural styles and personalized living spaces, catering to diverse aesthetic preferences and functional requirements.
Sustainability
Sustainability is a cornerstone of 3D-printed housing. The precision of 3D printing minimizes material waste, and the use of eco-friendly materials reduces the environmental impact of construction. Additionally, the potential for incorporating renewable energy systems and efficient insulation in the design further enhances the sustainability of these homes.
Real-World Examples of 3D-Printed Houses
ICON’s House Zero
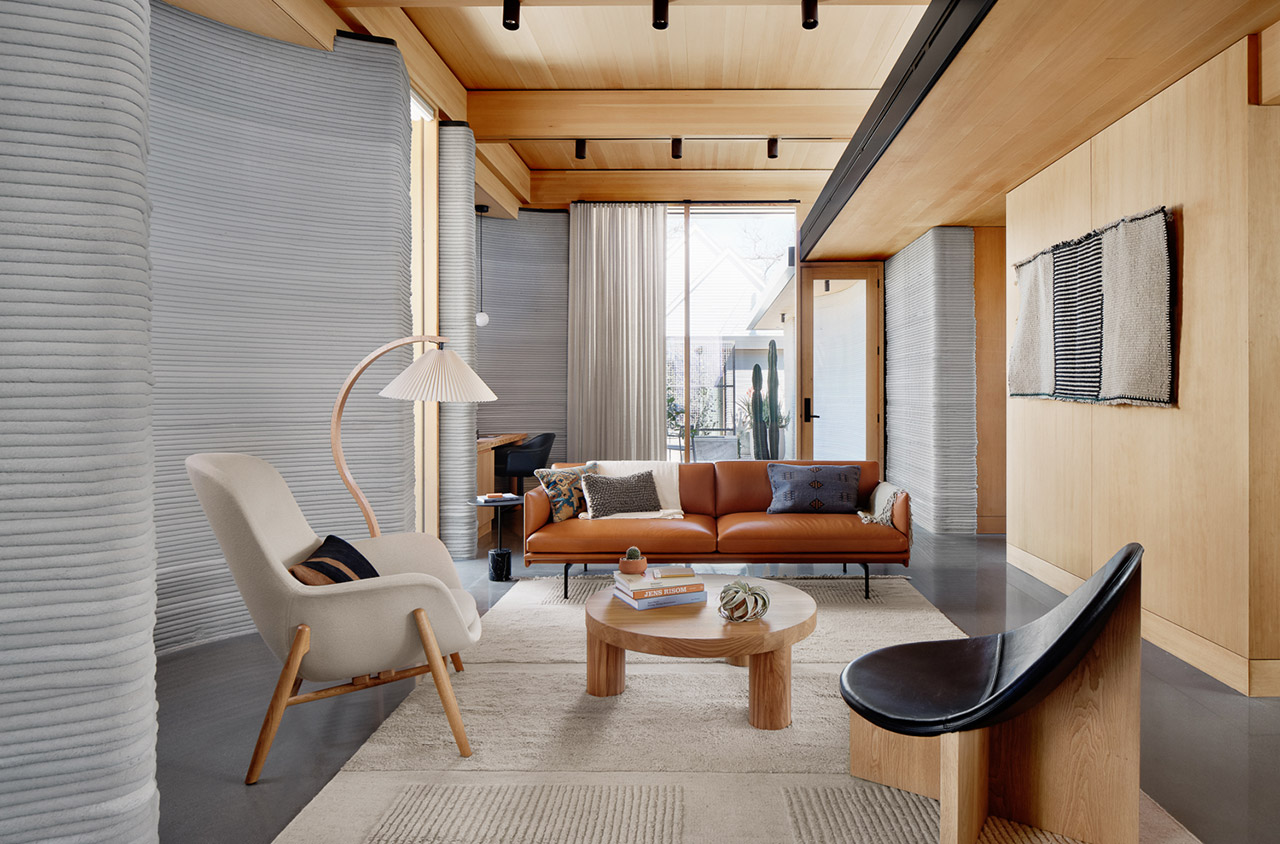
ICON, in partnership with Lake|Flato Architects, developed House Zero in Austin, Texas. The project showcased how 3D printing could be used to create large, custom homes. The 2,350-square-foot home was built using Lavacrete, a special concrete mixture designed for insulation and durability. Completed in under two weeks, House Zero demonstrates how 3D printing can help create sustainable, energy-efficient homes at scale.
ICON, in collaboration with Lake|Flato Architects, developed House Zero, a 2,350-square-foot home in Austin, Texas. The house features curved walls and is constructed using Lavacrete, a material designed for durability and insulation. Completed in under two weeks, House Zero exemplifies the potential of 3D printing in creating sustainable, energy-efficient homes.
Apis Cor’s 3D-Printed Home
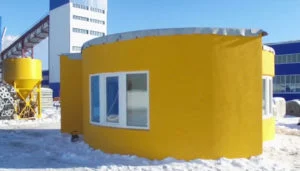
Apis Cor, a startup, built a 400-square-foot house in 24 hours using a mobile 3D printer. Located in the Moscow region, this affordable home costs just $10,134. The house features reinforced concrete walls and incorporates essential systems, including wiring and plumbing.
Apis Cor, a startup from San Francisco, successfully 3D-printed a 400-square-foot house in just 24 hours using a mobile 3D printer. Built in the Moscow region of Russia, the house is constructed with a concrete mixture designed to last 175 years. Apis Cor plans to offer these homes for $10,134, including all essential elements such as windows, doors, wiring, and plumbing.
Tecla House by WASP
Tecla House, created by WASP in Italy, made history as the world’s first 3D-printed house made entirely of earth-based materials. This sustainable 645-square-foot structure features curved walls and arched ceilings, blending modern 3D printing technology with traditional architecture. The Tecla project aims to tackle housing shortages while promoting sustainability.
The Tecla house, developed by Italian architecture studio Mario Cucinella Architects and 3D printing specialists WASP, is the world’s first 3D-printed house made entirely from a mixture of local earth and water. The 645-square-foot structure features curving walls and arched ceilings, combining ancient architectural styles with modern technology to address contemporary issues like climate change and housing shortages.
Use Cases and Problem Solving
3D-printed houses offer solutions to several critical issues in the housing industry:
- Affordable Housing: The reduced construction costs make homeownership more accessible to low-income families and individuals.
- Disaster Relief: The rapid construction capabilities allow for quick deployment of housing in disaster-stricken areas, providing immediate shelter to those in need.
- Sustainable Living: The use of eco-friendly materials and energy-efficient designs promotes sustainable living practices.
- Customization: The design flexibility enables the creation of homes tailored to individual preferences and requirements.
How to Buy and Where to Buy
Purchasing a 3D-printed house involves selecting a reputable 3D printing construction company and collaborating with them to design and build your home. Companies like ICON, Apis Cor, and WASP offer services in various regions. It’s essential to research each company’s offerings, review their portfolios, and consult with them to understand the process, costs, and timelines involved.
Frequently Asked Questions
Are 3D-printed houses safe and durable?
Yes, 3D-printed houses deliver strong safety and durability standards. Companies like Apis Cor have developed advanced concrete mixes that resist harsh environmental conditions and stand the test of time, lasting up to 175 years. Unlike traditional homes, these structures benefit from precise layering techniques that reduce construction flaws and reinforce structural integrity.
By using cutting-edge technology and specialized materials, 3D printing enhances long-term resilience. This innovation plays a crucial role in revolutionizing affordable and sustainable housing solutions, especially in areas facing climate challenges, material shortages, or housing crises.
Yes, 3D-printed houses offer impressive safety and durability. Companies like Apis Cor specifically engineer their concrete mixtures to withstand extreme conditions and last for decades, up to 175 years. These homes resist environmental stress such as temperature fluctuations, wind, and moisture. As a result, 3D-printed homes provide a long-lasting, secure shelter solution that supports the broader goal of revolutionizing affordable and sustainable housing solutions.
How long does it take to build a 3D-printed house?
Builders can complete many 3D-printed houses in as little as 24 to 48 hours. Compared to traditional construction, which often spans several months, this rapid pace offers a huge advantage, especially during emergencies or in areas with urgent housing needs. The speed of 3D printing directly contributes to affordable and sustainable housing solutions by lowering labor costs and accelerating deployment.
Where can I buy a 3D-printed house?
You can buy a 3D-printed home by contacting providers like ICON, Apis Cor, or WASP. These companies offer customizable designs and operate in various global markets. To get started, visit their websites, review their models, and request a consultation. Choosing one of these providers means actively investing in the revolution of sustainable housing solutions.